In today’s fast-paced and interconnected world, the ability to swiftly adapt and respond to unexpected events is crucial for maintaining robust supply chains. Vulnerabilities within these networks can lead to significant disruptions, affecting everything from production to customer satisfaction.
This is where the integration of Enterprise Resource Planning (ERP) systems becomes indispensable. ERP and supply chain management together form a resilient backbone that helps businesses navigate and manage crises effectively. By leveraging ERP systems, companies can not only streamline their day-to-day operations but also enhance their capabilities to anticipate, react to, and recover from various challenges that arise during crises. As we delve deeper into the role of ERP and supply chain management in crisis scenarios, it becomes clear how these technologies are not just tools for efficiency, but essential instruments for survival and continuity in tumultuous times.
Understanding supply chain vulnerabilities
Supply chains are intricate networks that involve multiple stakeholders, processes, and technologies. Some common vulnerabilities include:
-
Relying on a single supplier for critical materials can be highly risky, particularly if that supplier faces crises such as political instability, natural disasters, or financial issues. This dependency can create significant bottlenecks when the supplier fails to deliver.
Understanding these vulnerabilities and their potential impact during crises underscores the importance of integrating robust ERP and supply chain management systems. These systems play a crucial role in enhancing supply chain resilience, ensuring that businesses are better equipped to handle disruptions and maintain operational continuity.
How vulnerabilities affect supply chains during crises
During crises, these vulnerabilities can become critical pain points:
- Supply Disruptions: Without alternative sources or contingency plans in place, a disruption at a single source can halt production across the entire supply chain, leading to stock-outs, lost sales, and dissatisfied customers.
- Delayed Reactions: Manual and non-integrated systems delay the detection of and reaction to supply chain disruptions. This slow response time can exacerbate the impact of the disruption, leading to increased costs and extended recovery times.
- Operational Rigidity: Inflexible operations struggle to adapt to the rapid changes required during a crisis, leading to increased costs, decreased service levels, and potential loss of market share. This rigidity can prevent a company from taking advantage of emergent opportunities or avoiding escalating threats.
Enhancing resilience through proactive measures
To combat these vulnerabilities, companies need to take proactive steps:
- Diversifying suppliers: Building relationships with multiple suppliers for critical inputs can mitigate the risks associated with single sourcing.
- Investing in technology: Implementing modern ERP systems enhances data visibility and process automation, allowing for quicker responses to supply chain disruptions.
- Flexibility in operations: Developing flexible operational strategies, such as just-in-time manufacturing or dynamic rerouting of logistics, can help businesses adapt swiftly to changing conditions.
Understanding these vulnerabilities and their impact during crises underscores the importance of integrating robust ERP and supply chain management systems. These systems play a crucial role in enhancing supply chain resilience, ensuring that businesses are better equipped to handle disruptions and maintain operational continuity.
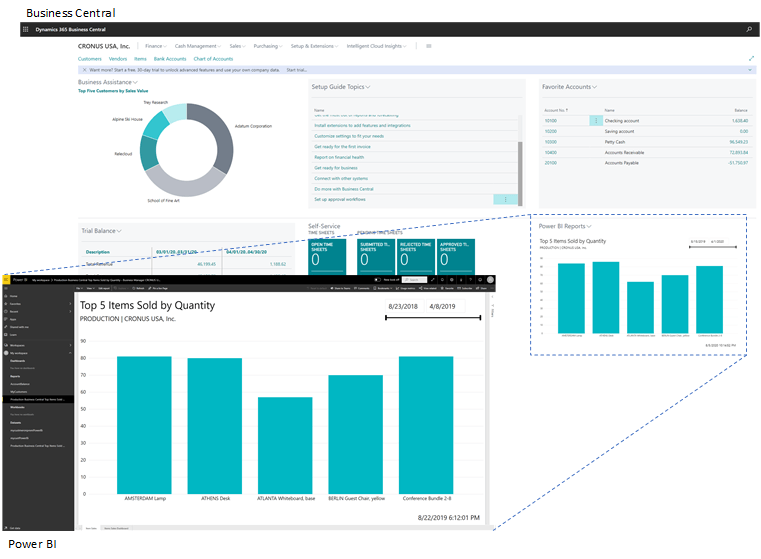
ERP features that support crisis management
Real-Time Data Access
One of the most crucial features of an ERP system in managing crises is its ability to provide real-time access to data across the entire supply chain. This capability allows companies to:
- Monitor Inventory Levels: Quickly identify shortages or surpluses and adjust orders accordingly.
- Track Shipments: Ensure that goods are moving as expected and identify potential delays before they become critical.
- View Supplier Status: Keep tabs on the operational status of suppliers and anticipate disruptions.
Scalability and Flexibility
ERP systems are designed to scale operations up or down based on current needs, which is invaluable in times of crisis. They allow businesses to:
- Adjust Production Schedules: Quickly reallocate resources or modify production lines to meet changing demands.
- Manage Resource Allocation: Efficiently redistribute tasks and resources to adapt to the crisis, ensuring that critical functions continue to operate.
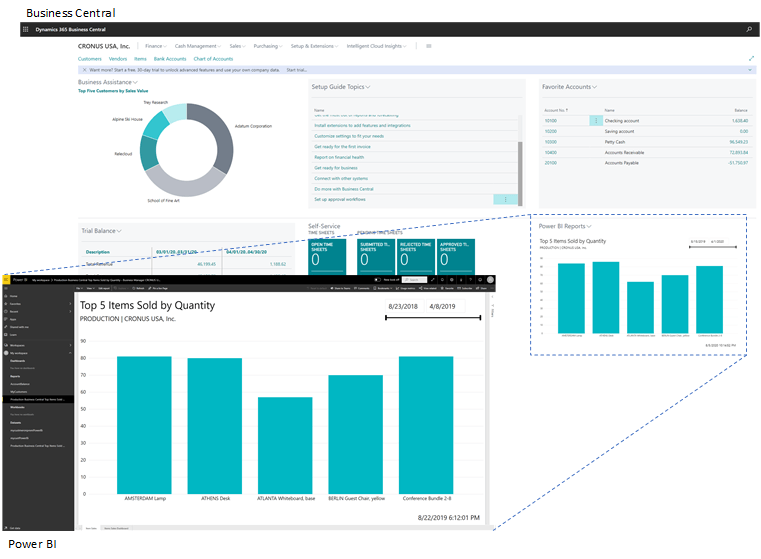
Integrated Communication Tools
Effective communication is essential during a crisis. ERP systems facilitate this by providing integrated communication tools that:
- Enhance Collaboration: Allow teams across different departments and locations to collaborate more effectively, ensuring everyone is on the same page.
- Improve Decision Making: Enable quicker decision-making by providing all stakeholders with the same timely and accurate information.
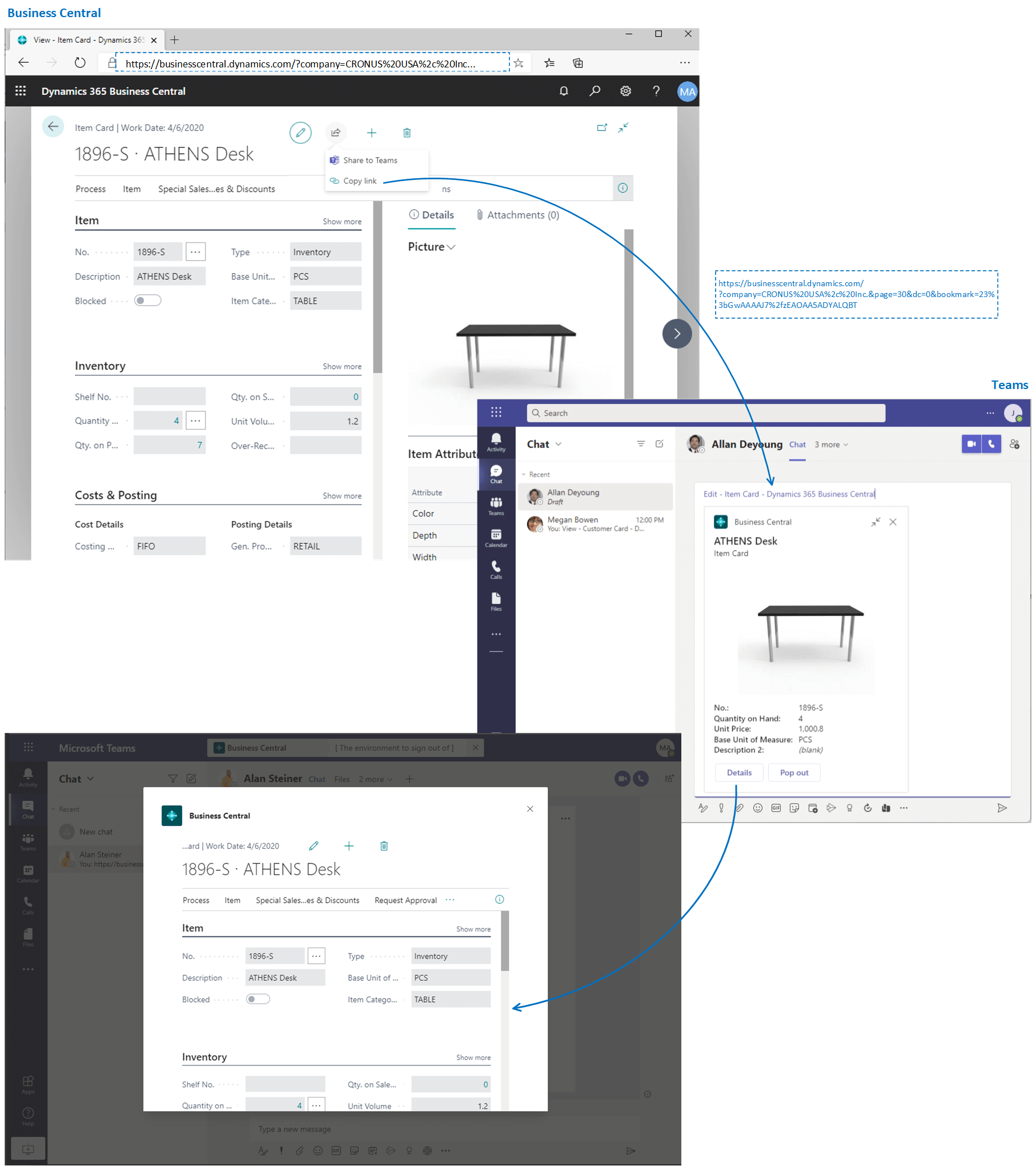
Automated Response Mechanisms
Automation is another key feature of ERP systems that aids in crisis management. It includes:
- Automated Alerts and Notifications: Send out warnings when inventory levels are low or if there are delays in the supply chain.
- Trigger-Based Actions: Set up triggers to automatically reorder stock, reroute shipments, or initiate other pre-defined actions without human intervention.
Advanced Analytics and Reporting
ERP systems come equipped with advanced analytics and reporting tools that can forecast and analyze trends to better prepare for future crises. These tools help in:
- Predictive Analysis: Use historical data to predict potential future disruptions and plan accordingly.
- Performance Reporting: Generate detailed reports on various aspects of the supply chain to identify areas of risk and opportunity.
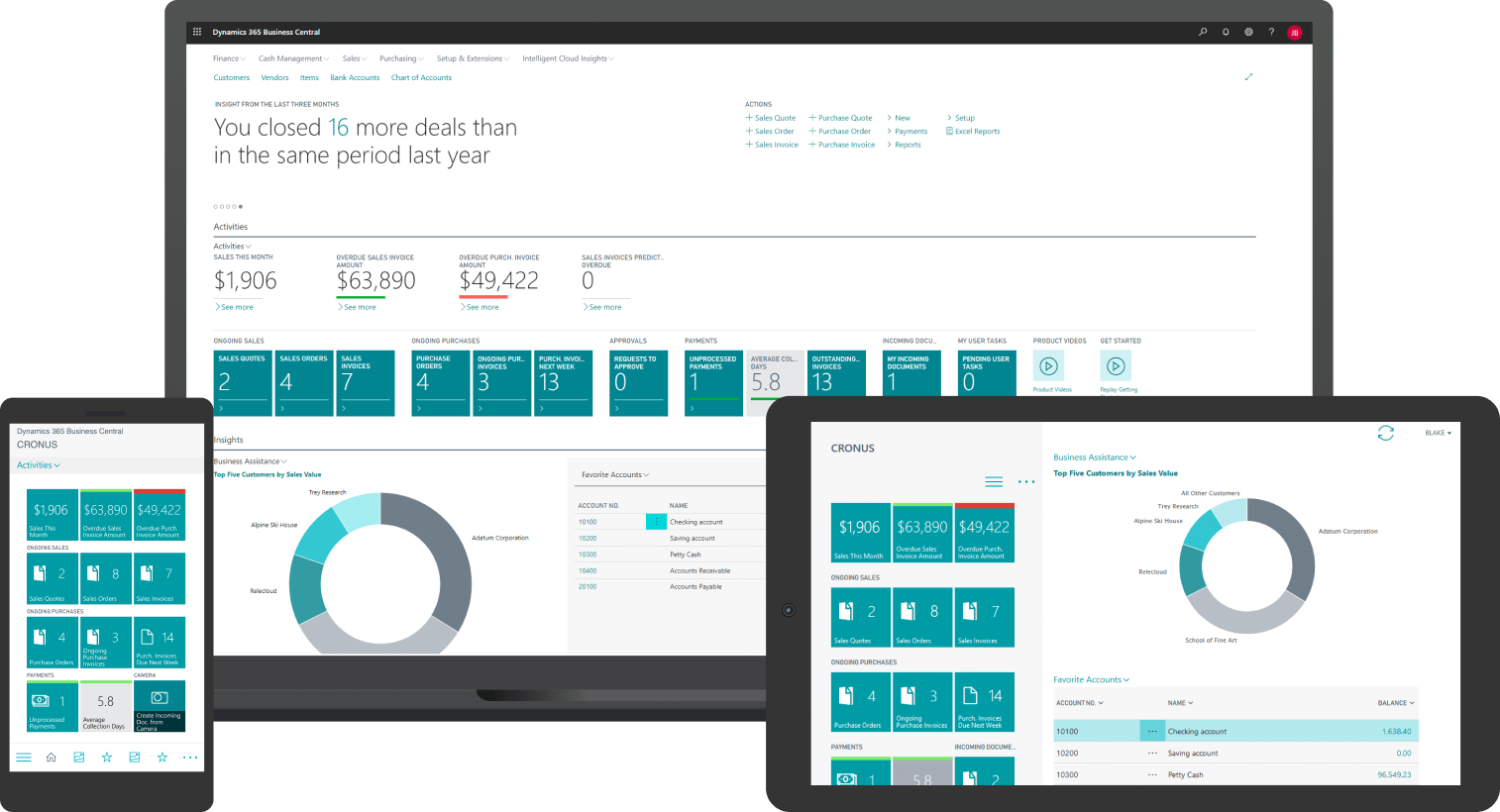
Enhanced Security Features
Security is a critical aspect of crisis management, and ERP systems provide robust security features to protect sensitive data and operations. These features include:
- Data Encryption: Ensure that all data transmitted and stored within the ERP system is securely encrypted.
- Access Controls: Restrict access to sensitive information to authorized personnel only, minimizing the risk of data breaches.
Scenario Planning and Simulation
ERP systems can model various crisis scenarios to help companies prepare response strategies. This feature allows for:
- Impact Simulation: Simulate the impact of potential crises on different areas of the supply chain.
- Strategy Testing: Test different response strategies to find the most effective approach for various scenarios.
These additional ERP features enhance the system's capability to manage and mitigate crises by providing comprehensive tools for prediction, security, and strategic planning. By leveraging these capabilities, companies can ensure that their supply chains are not only resilient but also adaptive to rapidly changing circumstances.
Strategies for leveraging ERP for crisis preparedness
Proactive planning features
ERP systems offer a range of proactive planning tools that enable businesses to prepare for potential crises before they occur. These tools include:
- Demand Forecasting: Utilize historical data and predictive analytics to forecast future demand under various scenarios, allowing for better inventory management and resource allocation.
- Inventory Optimization: Implement algorithms to determine optimal inventory levels that balance the cost of holding stock against the risk of stockouts, particularly in unpredictable conditions.
Training and Simulation Tools
Preparedness also involves ensuring that personnel are ready to handle crisis situations. ERP systems can aid in this area through:
- Crisis Simulation Exercises: Conduct simulations of different crisis scenarios to help teams practice their response strategies, making them more effective in real situations.
- Training Modules: Offer training modules integrated within the ERP system to keep staff updated on the latest crisis management protocols and system functionalities.
Building Resilience Through Integration
Integrating ERP systems with other business management tools and technologies can enhance overall resilience:
- Integration with External Data Sources: Connect the ERP system with external data sources like market trends, weather forecasts, or geopolitical news to stay informed about potential risks.
- Seamless Connectivity with Other Business Tools: Ensure ERP systems work seamlessly with other critical business systems, such as Customer Relationship Management (CRM) or Human Resources Management Systems (HRMS), to maintain business continuity.
Continuous Improvement and Feedback Loops
To stay ahead in crisis management, continuous improvement processes embedded in ERP systems are essential:
- Feedback Mechanisms: Implement feedback loops that allow for the continuous collection and analysis of data regarding the effectiveness of crisis response strategies.
- Iterative Updates: Regularly update the ERP system based on feedback and new information to improve its crisis management capabilities.
Utilizing ERP Dashboards for Monitoring and Alerts
ERP dashboards can be critical in monitoring the health of your supply chain and alerting you to potential issues before they escalate:
- Customizable Dashboards: Use ERP dashboards to monitor key performance indicators (KPIs) relevant to crisis management.
- Real-Time Alerts: Set up real-time alerts for critical thresholds to prompt immediate action, preventing small issues from turning into larger crises.
These strategic approaches to leveraging ERP for crisis preparedness not only enhance a company’s resilience but also empower it to act swiftly and effectively, minimizing the impact of disruptions on the supply chain.
The Role of Data Analytics and AI in Crisis Response
Enhancing Predictive Capabilities with AI
Artificial Intelligence (AI) integrated into ERP systems can transform how businesses anticipate and respond to supply chain disruptions. Key capabilities include:
- Predictive Analytics: Utilize AI to analyze vast amounts of data and predict potential disruptions before they occur. This can include predicting supplier failures, transportation delays, or demand spikes.
- Machine Learning Models: Deploy machine learning models that continuously learn from historical data and improve their predictions over time, making the ERP system smarter and more responsive.
Automating Decision-Making Processes
AI can also automate complex decision-making processes during crises, reducing the time and effort required to respond effectively:
- Automated Problem Solving: Set up AI algorithms to automatically identify the best solutions or alternatives when disruptions occur, such as finding the next best supplier or optimizing rerouting options for deliveries.
- Dynamic Replanning: Use AI to dynamically adjust plans and schedules in real-time as new information becomes available, ensuring that operations remain as efficient as possible under changing conditions.
Data-Driven Insights for Strategic Decisions
The integration of advanced data analytics in ERP systems provides strategic insights that can guide decision-making during a crisis:
- Risk Assessment Tools: Implement tools to assess and quantify risks associated with different parts of the supply chain, allowing companies to prioritize their response efforts where they are needed most.
- Scenario Analysis: Conduct scenario analysis to understand the potential impact of various crisis situations and develop appropriate strategies based on data-driven insights.
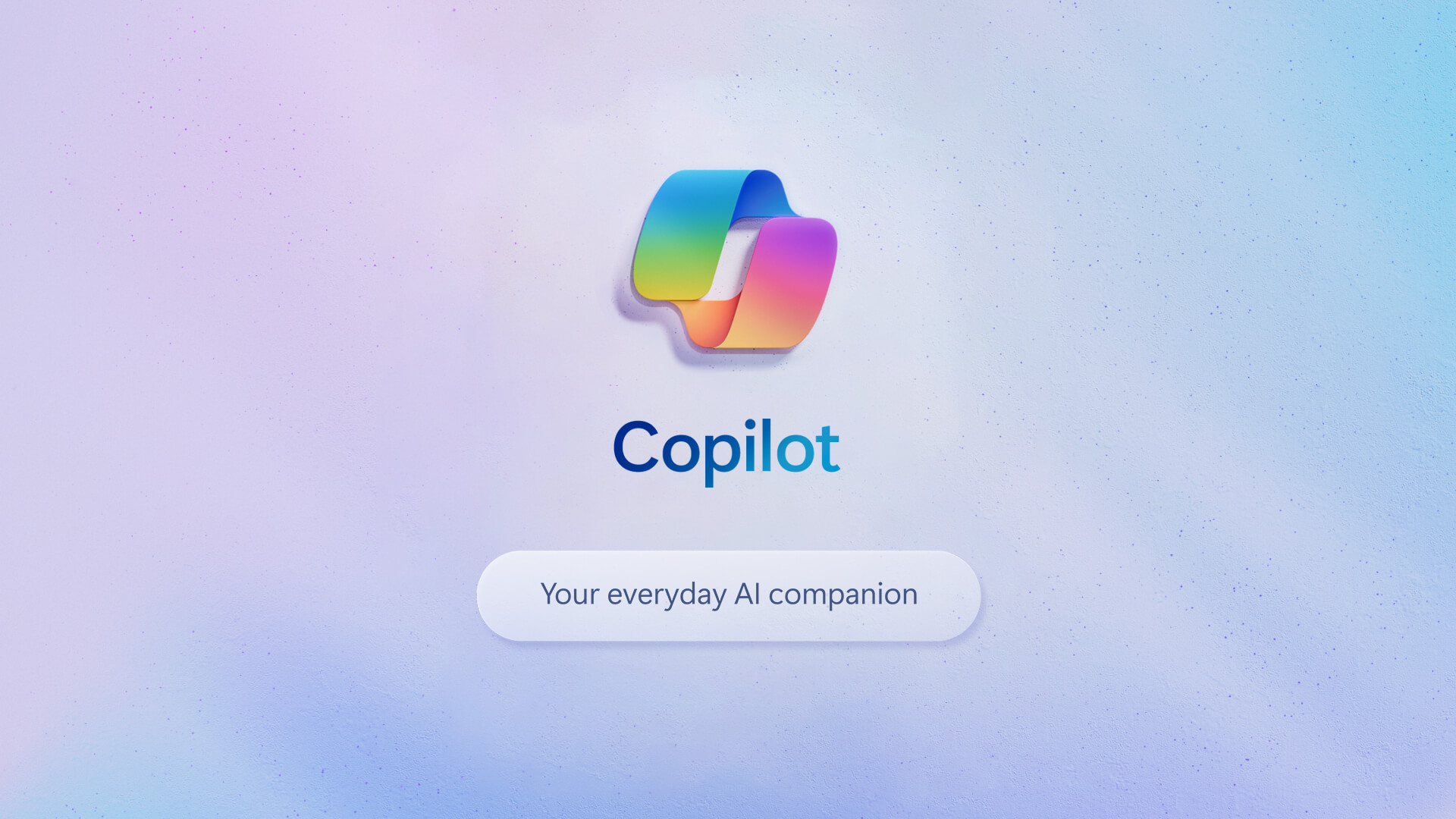
Integrating Copilot into Business Central for Enhanced AI Capabilities
Microsoft’s introduction of Copilot into Business Central brings advanced AI capabilities that significantly enhance crisis management within ERP systems:
- Natural Language Processing (NLP): Copilot can interpret user queries in natural language, allowing users to obtain information and generate reports quickly and intuitively.
- Automated Insights: Copilot provides automated insights into business operations, highlighting potential issues and opportunities without requiring manual analysis.
- Enhanced User Assistance: Through its AI-driven interface, Copilot can offer proactive suggestions for optimizing workflows and improving efficiency, particularly valuable during high-pressure crisis situations.
Enhancing Operational Visibility
ERP systems equipped with AI and analytics improve visibility across all stages of the supply chain, which is crucial during disruptions:
- Real-Time Tracking and Visualization: Employ visualization tools that provide a graphical view of the entire supply chain, making it easier to identify problem areas and intervene quickly.
- Performance Monitoring: Use analytics to monitor the performance of various supply chain components, ensuring that any deviations from expected performance can be addressed promptly.
Continuous Learning and Adaptation
AI not only supports immediate crisis response but also helps businesses adapt and evolve by learning from each incident:
- Feedback Loops and Learning Algorithms: Incorporate feedback loops that allow the system to learn from each crisis, improving its responses to future disruptions.
- Knowledge Sharing: Facilitate knowledge sharing across the organization, enabling different departments to benefit from insights gained during past crises.
The inclusion of AI technologies like Copilot in Business Central significantly bolsters a company’s ability to navigate complex and rapidly evolving crisis scenarios within their supply chain, ensuring they remain resilient and responsive in the face of disruptions.
Solutions to navigate challenges and drive digital transformation
Insights from our manufacturing white paper
Future Directions in ERP for Enhancing Crisis Resilience
Embracing Emerging Technologies
The future of ERP systems in enhancing supply chain crisis resilience lies in the continuous integration of cutting-edge technologies. Key areas of technological advancements include:
- Blockchain Technology: Incorporate blockchain to ensure transparency and traceability in the supply chain. This can help verify the authenticity of goods and secure transactions against fraud, particularly in crisis scenarios.
- Internet of Things (IoT): More extensive use of IoT devices can provide real-time data from every corner of the supply chain, from production lines to delivery routes, enhancing visibility and responsiveness.
- Advanced Robotics and Automation: Implement robotics to handle critical operations, reducing human error and maintaining productivity during disruptions.
Integration with Other Digital Ecosystems
As digital transformation accelerates, ERP systems will need to seamlessly integrate with other digital ecosystems to provide a holistic view and response capability across all business operations:
- Cross-Platform Integration: Ensure ERP systems can communicate with various digital platforms and software solutions, from CRM systems to advanced analytics tools, creating a cohesive technology ecosystem.
- Cloud-Based Solutions: Increase the adoption of cloud-based ERP solutions to enhance flexibility, scalability, and remote accessibility, essential features for managing crises effectively.
Personalized and Predictive ERP Systems
Future ERP systems will likely focus more on personalization and predictive capabilities to cater to specific industry needs and preempt potential crises:
- Customization: More advanced customization options to tailor ERP functionalities to the specific dynamics and risks of different industries.
- Predictive Intelligence: Enhanced predictive intelligence capabilities to foresee potential disruptions based on external data inputs like market trends, political changes, or environmental factors.
Sustainability and Social Responsibility
Sustainability will play an increasing role in the development of ERP systems as businesses become more aware of their environmental impact and social responsibilities:
- Sustainable Supply Chain Management: ERP systems that help manage and optimize for sustainability, such as minimizing waste, optimizing energy use, and ensuring ethical sourcing practices.
- Compliance and Reporting: Improved tools for tracking compliance with local and international regulations, and for reporting on sustainability metrics and corporate social responsibility initiatives.
Enhanced Training and Support
As ERP systems evolve, so too must the training and support provided to ensure that all users can leverage these complex tools effectively:
- Interactive Training Modules: Development of more interactive, AI-driven training modules that adapt to the user’s learning pace and style.
- Real-Time Support Systems: Enhanced support systems, possibly powered by AI, that provide real-time assistance and troubleshooting to resolve issues swiftly and prevent potential crises.
These future directions for ERP systems emphasize not only technological advancement but also a commitment to making ERP solutions more robust, intuitive, and aligned with broader business and societal goals. As these systems evolve, they will become even more indispensable tools for companies seeking to enhance their resilience and manage supply chains more effectively during crises.
Strengthening Supply Chain Resilience with ERP Systems
Recap of Key Points
In this article, we've explored the vital role that ERP and supply chain management plays in enhancing supply chain resilience, particularly in the face of crises. From providing real-time data access and scalable operations to integrating cutting-edge technologies like AI and blockchain, ERP systems are fundamental tools for ensuring that businesses can anticipate, respond to, and recover from disruptions.
The Importance of Proactive ERP Integration
It is clear that merely reacting to crises is no longer sufficient. Businesses must proactively integrate ERP systems into their core operations to build a robust and responsive supply chain. This involves not only adopting the technology but also continuously updating and refining ERP capabilities to address evolving challenges and leverage new opportunities.
Encouraging Continuous Improvement and Adaptation
The landscape of supply chain management is continually changing, and so too must the tools we use to manage it. Businesses should view their ERP systems not just as a solution for today but as a platform for continuous improvement. Leveraging the full capabilities of ERP, including ongoing updates and advancements in technology, is crucial for maintaining competitiveness and resilience.
Implementing and optimizing an ERP system is a significant investment in time and resources, but the payoff is a more adaptable, efficient, and resilient supply chain. As we look to the future, the integration of advanced technologies and strategies within ERP systems will continue to be a key driver in managing supply chain risks and ensuring business continuity in uncertain times.
Ready to Enhance Your Supply Chain Resilience?
Don’t let supply chain vulnerabilities disrupt your business operations. Contact us today to discover how our ERP solutions can fortify your supply chain, streamline your processes, and prepare you for the unexpected. Our experts are ready to help you implement a system that not only meets your current needs but also adapowers your business for future challenges.
Liked what you just read? Sharing is caring.
June 25, 2024 by Arianne Pellerin by Arianne Pellerin Marketing Specialist
Driven by an unwavering obsession to optimize processes and revolutionize marketing with innovative ideas, I never stop searching for the perfect solution. My true passion lies in crafting dreamlike experiences by harnessing the full potential of web analytics and cutting-edge digital strategies. As a blog writer for Gestisoft, I bring this expertise to the forefront, focusing primarily on our ERP solutions.