Introduction
In the ever-evolving landscape of manufacturing, staying competitive requires more than just producing quality products. It demands an agile and efficient approach that optimizes operations at every level. Enter Manufacturing ERP (Enterprise Resource Planning) systems — the digital backbone of modern manufacturing facilities.
This article explores the remarkable impact of Manufacturing ERP systems on the industry, uncovering 20 key benefits that can revolutionize the way manufacturing operations are conducted. Whether you're a seasoned manufacturing professional or just stepping into the world of ERP solutions, this comprehensive guide will shed light on how ERP systems can streamline processes, enhance decision-making, and ultimately drive success.
The Role of Manufacturing ERP Systems
Manufacturing ERP systems are software solutions designed specifically for the complex needs of manufacturing businesses. These systems integrate and centralize various facets of operations, from production and inventory management to supply chain coordination and beyond. By offering a unified platform for data management, communication, and analysis, ERP systems empower manufacturers to make informed decisions, respond swiftly to market changes, and optimize resources for maximum efficiency.
Purpose and Scope of the Article
The purpose of this article is to delve deep into the multifaceted benefits of Manufacturing ERP systems. Whether you are considering implementing an ERP system for the first time or seeking to maximize the potential of your existing one, this guide will provide valuable insights into the transformative capabilities of these solutions.
We will explore each benefit in detail, providing real-world examples and practical advice on how to leverage ERP systems for success. From streamlining production processes and enhancing supply chain management to improving quality control and increasing cost efficiency, you'll discover the wide-ranging advantages that ERP systems bring to the manufacturing table.
So, if you're ready to embark on a journey through the world of Manufacturing ERP systems and their impact on optimizing operations, let's dive in and explore the first of these 20 benefits: Streamlining Production Processes.
Streamlining Production Processes
Manufacturing ERP systems are catalysts for transforming how production processes are managed and executed. They bring a level of precision, efficiency, and visibility that is hard to achieve through traditional methods. In this section, we'll explore how ERP systems optimize production processes, enhancing your manufacturing capabilities.
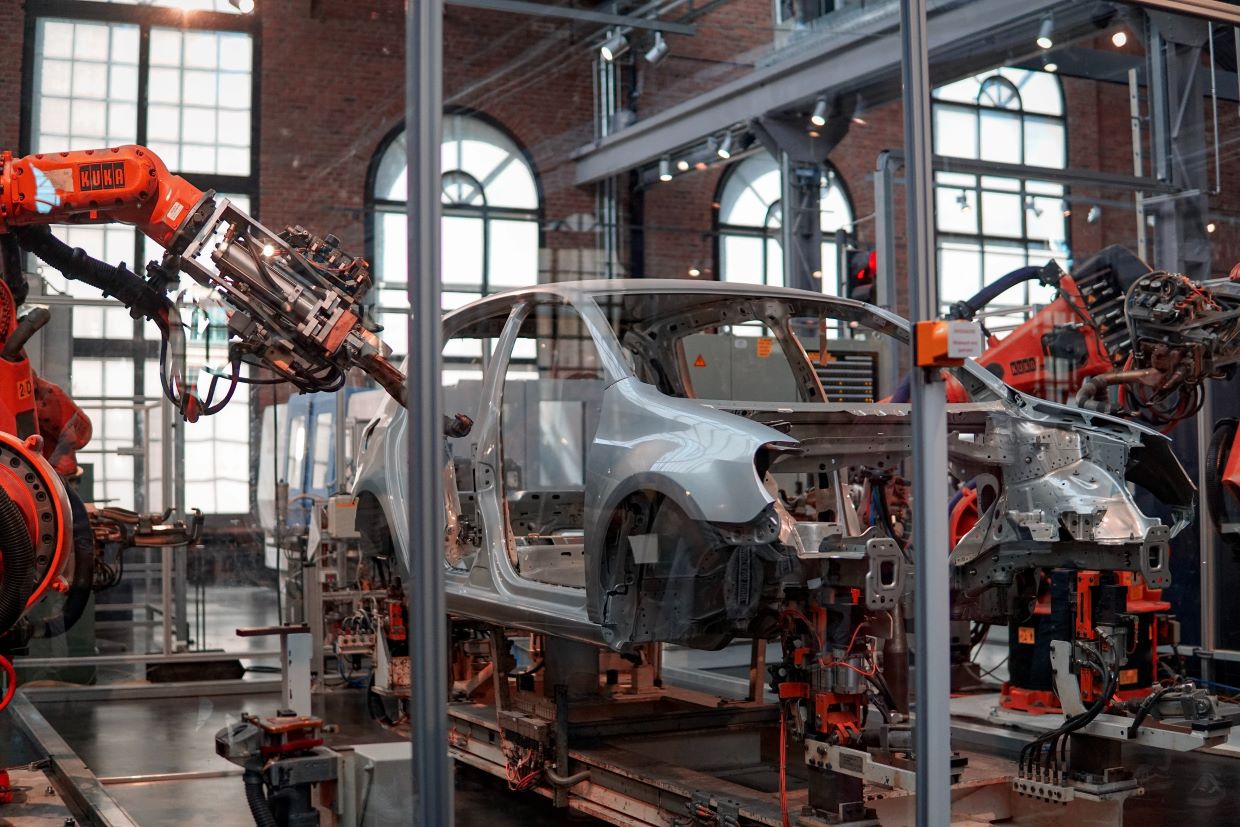
1. Real-time Production Monitoring
One of the standout benefits of ERP systems in manufacturing is the ability to monitor production in real-time. Traditionally, tracking the progress of manufacturing orders and production schedules could be a cumbersome and manual process. With ERP systems in place, every aspect of production can be monitored from a centralized dashboard.
- Instant Status Updates: ERP systems provide instant updates on the status of production orders, allowing you to see which orders are in progress, completed, or delayed. This real-time visibility enables you to make quick decisions to address any bottlenecks or delays.
- Resource Allocation: Through real-time monitoring, you can optimize resource allocation. If a machine is underutilized, it can be quickly reassigned to another task, reducing downtime and increasing overall efficiency.
- Quality Control: Monitoring production in real-time also facilitates quality control. If a product does not meet quality standards, it can be identified and addressed immediately, preventing defective products from reaching customers.
2. Inventory Management
Effective inventory management is crucial for any manufacturing operation, as excess inventory ties up capital and insufficient inventory can lead to production delays. ERP systems offer a range of features to optimize inventory management:
- Inventory Tracking: ERP systems track the movement of raw materials, work-in-progress (WIP), and finished goods in real-time. This ensures that you always have accurate inventory levels, reducing the risk of overstocking or understocking.
- Automated Reordering: With ERP systems, you can set up automated reorder points for raw materials. When inventory falls below a certain threshold, the system can generate purchase orders, ensuring that you never run out of essential materials.
- Cost Control: By managing inventory effectively, you can control costs associated with storage and carrying excess stock. This leads to cost savings over time.
3. Work Order Automation
Work orders are the backbone of manufacturing, detailing the steps and resources required to produce a product. ERP systems automate the creation and management of work orders, streamlining the entire process:
- Efficient Work Order Generation: ERP systems can automatically generate work orders based on customer orders or sales forecasts. This reduces the time and effort required to initiate production.
- Resource Allocation: Work orders specify the resources needed for production, including labor, equipment, and materials. ERP systems help optimize resource allocation by ensuring that the right resources are available when needed.
- Scheduling: ERP systems enable efficient scheduling of work orders, taking into account resource availability and delivery deadlines. This ensures that production stays on track and that customer orders are fulfilled on time.
By streamlining production processes through real-time monitoring, effective inventory management, and work order automation, Manufacturing ERP systems contribute significantly to operational efficiency and cost reduction. In the next section, we'll explore how ERP systems enhance Supply Chain Management.
Enhancing Supply Chain Management
In the world of manufacturing, an efficient and well-managed supply chain can make all the difference. Manufacturing ERP systems play a pivotal role in enhancing supply chain management, ensuring that materials flow seamlessly from suppliers to production lines and ultimately to customers. In this section, we'll explore how ERP systems optimize supply chain management and bring numerous benefits to manufacturing businesses.
4. Supplier Collaboration
Effective collaboration with suppliers is essential for a smooth supply chain, and Manufacturing ERP systems facilitate this collaboration in several ways:
- Supplier Portals: ERP systems often come with supplier portals, where suppliers can access real-time information on inventory levels, production schedules, and order statuses. This transparency enables suppliers to plan their own operations more effectively.
- Automated Ordering: ERP systems can automate the ordering process, sending purchase orders to suppliers based on inventory levels and production requirements. This reduces the risk of stockouts and ensures a steady supply of materials.
- Quality Assurance: ERP systems can also track the quality of materials received from suppliers. If a supplier consistently delivers subpar materials, the system can flag this, allowing for supplier evaluation and potential corrective actions.
5. Demand Forecasting
Accurate demand forecasting is a cornerstone of effective supply chain management, and ERP systems provide powerful tools for this purpose:
- Historical Data Analysis: ERP systems can analyze historical sales data and market trends to generate accurate demand forecasts. This information helps in making informed decisions about production schedules and inventory levels.
- Scenario Planning: With ERP systems, you can perform "what-if" scenarios to assess the impact of different demand scenarios. This flexibility enables better preparation for fluctuations in demand.
- Inventory Optimization: By aligning production with demand forecasts, ERP systems help optimize inventory levels. This means you can avoid overstocking or understocking, reducing carrying costs and improving cash flow.
6. Inventory Optimization
Optimizing inventory levels is a critical aspect of supply chain management, and ERP systems provide the tools to do this effectively:
- Just-In-Time (JIT) Inventory: ERP systems can implement JIT inventory strategies, where materials are ordered and received just in time for production. This minimizes holding costs and reduces waste.
- Multi-Warehouse Management: For manufacturing operations with multiple warehouses, ERP systems offer centralized control and visibility over inventory across all locations. This ensures that materials are used efficiently and prevents excess stock.
- Inventory Valuation: ERP systems provide accurate inventory valuation methods, such as FIFO (First-In, First-Out) or LIFO (Last-In, First-Out), helping with financial reporting and cost analysis.
By enhancing supplier collaboration, improving demand forecasting, and optimizing inventory, Manufacturing ERP systems empower manufacturers to build more resilient and efficient supply chains. In the next section, we'll delve into how ERP systems improve quality control within manufacturing processes.
Improving Quality Control
In the manufacturing industry, ensuring product quality is paramount. Manufacturing ERP systems offer robust tools and features that enhance quality control efforts, helping manufacturers consistently deliver products that meet or exceed customer expectations. In this section, we'll explore how ERP systems contribute to improving quality control in manufacturing processes.
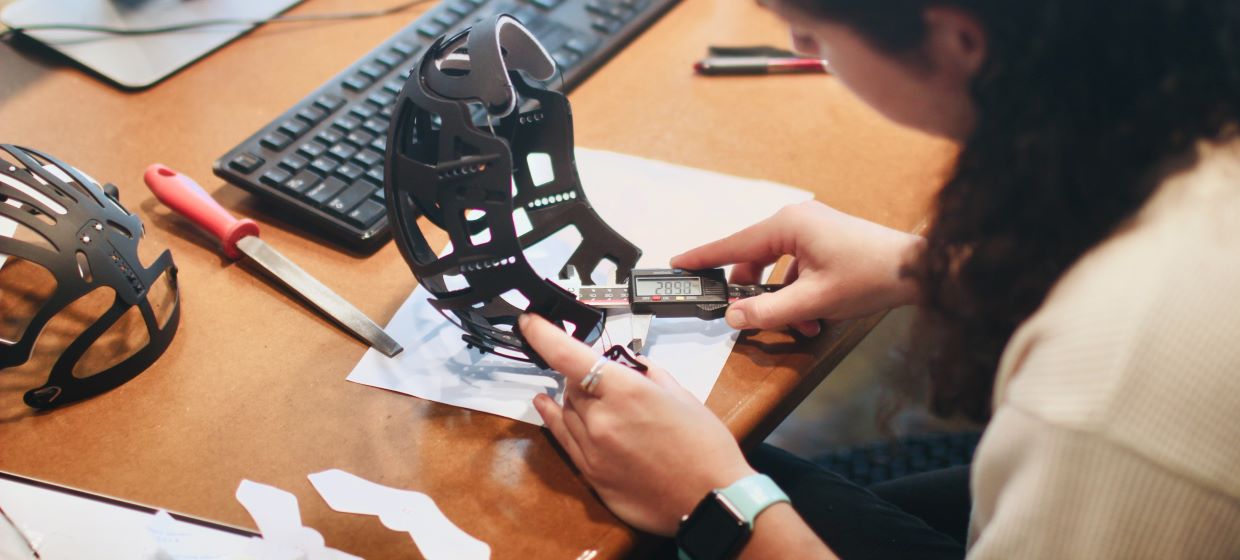
7. Quality Assurance Modules
Manufacturing ERP systems often include dedicated quality assurance modules, designed to enforce quality standards and track the quality of products at every stage of production:
- Quality Standards Compliance: ERP systems allow you to define and enforce quality standards and specifications for each product. These standards are consistently applied throughout production, reducing the risk of defects.
- Real-time Inspection: Quality assurance modules enable real-time inspection and testing of products as they move through the production process. Any deviations from quality standards are immediately flagged, allowing for corrective actions.
- Documentation and Traceability: ERP systems facilitate the documentation of quality control processes and provide traceability. This means you can trace the origin and quality history of each product, essential for compliance and recalls.
8. Traceability and Recall Management
The ability to trace products through the supply chain is crucial for quality control and compliance, and ERP systems excel in this area:
- Lot and Serial Number Tracking: ERP systems can assign unique lot or serial numbers to products, making it easy to trace their journey from raw materials to the end customer. This is particularly important for industries with stringent regulatory requirements.
- Recall Management: In the event of a product recall, ERP systems streamline the process. They can quickly identify affected products, their distribution, and their customers, enabling swift and targeted recalls, which minimizes damage to the brand and public safety risks.
- Root Cause Analysis: When quality issues arise, ERP systems provide data for root cause analysis. This helps in identifying and addressing the underlying causes to prevent similar issues in the future.
By incorporating quality assurance modules and robust traceability features, Manufacturing ERP systems empower manufacturers to maintain consistent product quality, reduce defects, and respond effectively to quality-related challenges. In the next section, we'll delve into how ERP systems increase cost efficiency within manufacturing operations.
Increasing Cost Efficiency
Cost efficiency is a critical aspect of successful manufacturing operations. Manufacturing ERP systems are designed to optimize resource allocation, reduce waste, and ultimately increase cost efficiency. In this section, we'll explore how ERP systems can help manufacturers achieve significant cost savings.
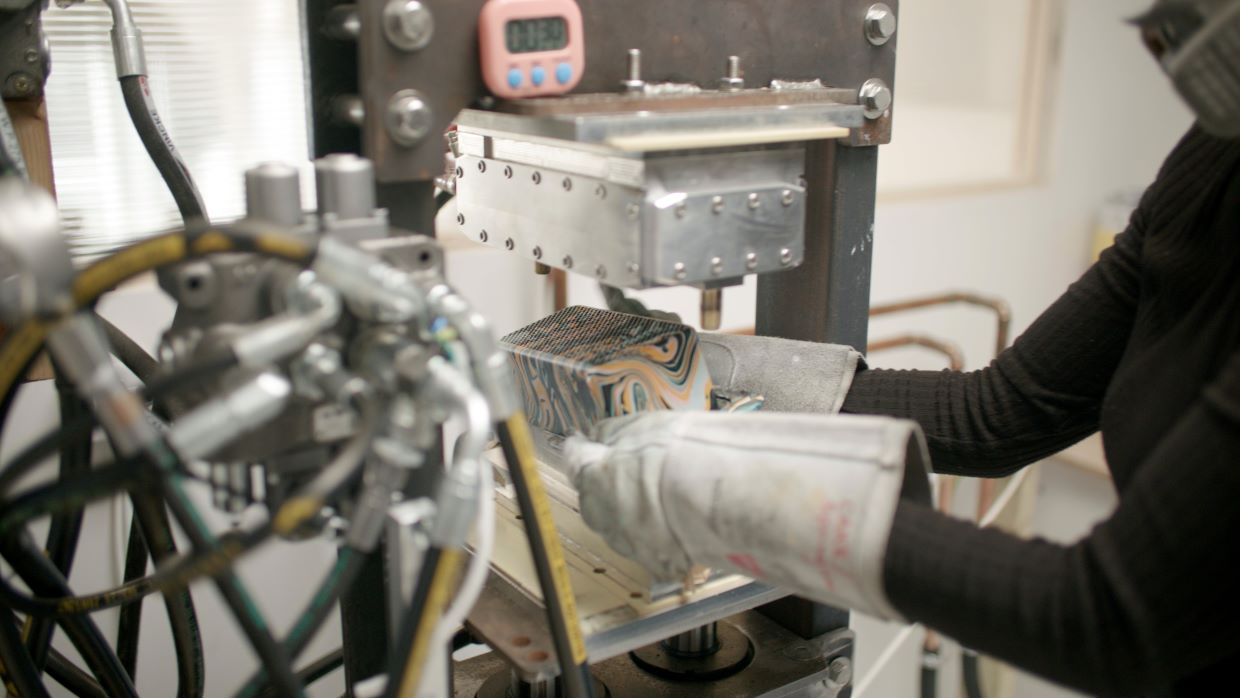
9. Cost Tracking and Analysis
Effective cost tracking and analysis are fundamental to cost efficiency, and ERP systems provide the tools needed for meticulous financial management:
- Cost Allocation: ERP systems enable the allocation of costs to specific products or production processes. This allows manufacturers to understand the true cost of producing each item, helping in pricing strategies and cost control.
- Budget Management: ERP systems often include budget management features, allowing you to set and track budgets for different aspects of your manufacturing operations. This prevents overspending and aligns financial goals with actual performance.
- Variance Analysis: ERP systems provide variance analysis tools that help identify discrepancies between planned and actual costs. This enables prompt action to address cost overruns and maintain profitability.
10. Resource Allocation
Efficient resource allocation is a cornerstone of cost efficiency, and ERP systems facilitate this by providing real-time visibility into resource availability and usage:
- Labor Optimization: ERP systems track labor hours and skills required for various tasks. This data helps in optimizing workforce allocation, ensuring that skilled employees are deployed where they are most needed.
- Equipment Utilization: ERP systems monitor the utilization of machinery and equipment. By identifying underutilized equipment or equipment breakdowns, you can reduce downtime and maintenance costs.
- Material Efficiency: With real-time inventory data and automated reordering, ERP systems prevent material shortages and overstocking, leading to cost savings in material procurement and storage.
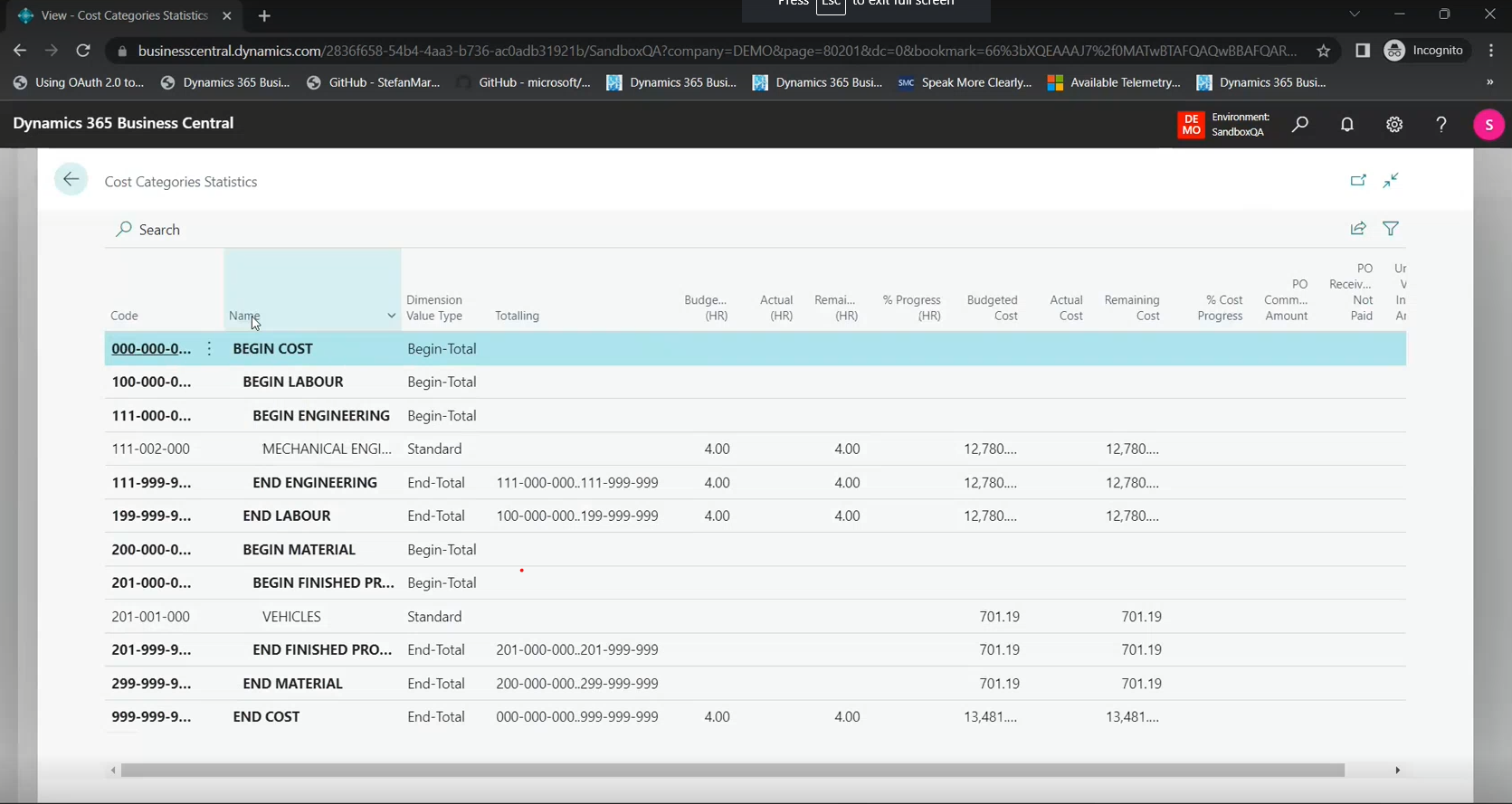
11. Cost Control
Cost control measures are integral to improving cost efficiency, and ERP systems offer mechanisms to implement and monitor these measures:
- Expense Monitoring: ERP systems provide detailed expense tracking, allowing you to identify areas where costs can be reduced. This may include identifying unnecessary expenditures or opportunities for bulk purchasing to secure discounts.
- Process Optimization: Through real-time data and analytics, ERP systems identify inefficiencies in manufacturing processes. By optimizing these processes, you can reduce production costs and improve overall efficiency.
- Energy Management: Some ERP systems include energy management modules, helping manufacturers monitor and reduce energy consumption, leading to substantial savings in utility bills.
Manufacturing ERP systems play a pivotal role in cost efficiency by providing the tools and data needed to make informed decisions, allocate resources efficiently, and implement cost control measures. In the next section, we'll explore how ERP systems boost productivity within manufacturing operations.
Boosting Productivity
Productivity is the lifeblood of manufacturing operations, and Manufacturing ERP systems are adept at streamlining processes, automating tasks, and maximizing workforce efficiency. In this section, we'll delve into how ERP systems contribute to boosting productivity within manufacturing organizations.
12. Workforce Management
Effective workforce management is central to productivity improvement, and ERP systems offer tools to optimize workforce allocation and performance:
- Resource Scheduling: ERP systems enable efficient scheduling of labor resources. You can match the right employees with the right tasks, reducing downtime and improving overall efficiency.
- Skills Tracking: ERP systems often include employee skill tracking features, helping you identify employees with specific skills needed for particular tasks. This ensures that tasks are assigned to the most qualified individuals.
- Time and Attendance Tracking: ERP systems simplify time and attendance tracking, reducing administrative work. This data is essential for accurate payroll and workforce analysis.
13. Automated Reporting
Reporting is a critical aspect of manufacturing operations, and ERP systems automate the generation of various reports, enhancing productivity in several ways:
- Real-time Reporting: ERP systems provide real-time access to key performance indicators (KPIs) and reports. This means decision-makers have access to up-to-date information to make timely and informed choices.
- Custom Report Generation: Users can create custom reports tailored to their specific needs without requiring IT intervention. This flexibility enables individuals at all levels of the organization to access the data they require.
- Data Accuracy: Automated reporting reduces the risk of human error in data entry and reporting. This ensures that decisions are based on accurate and reliable information.
14. Continuous Improvement
ERP systems support a culture of continuous improvement, a cornerstone of productivity enhancement:
- Data for Analysis: ERP systems provide a wealth of data that can be analyzed to identify bottlenecks, inefficiencies, and areas for improvement. This data-driven approach streamlines processes and reduces waste.
- Feedback Loops: ERP systems enable feedback loops where employees can provide input on process improvements and suggest changes. This encourages collaboration and innovation within the organization.
- Benchmarking: ERP systems facilitate benchmarking against industry standards and best practices. This helps organizations set productivity goals and track their progress.
By optimizing workforce management, automating reporting, and fostering a culture of continuous improvement, Manufacturing ERP systems empower manufacturers to boost productivity, reduce operational costs, and ultimately enhance their competitive edge. In the next section, we'll explore how ERP systems accelerate time-to-market for products.
Accelerating Time-to-Market
In today's fast-paced business environment, the ability to bring new products to market quickly is a competitive advantage. Manufacturing ERP systems play a crucial role in streamlining product development and launch processes, helping manufacturers accelerate their time-to-market. In this section, we'll explore how ERP systems contribute to faster product development and introduction.
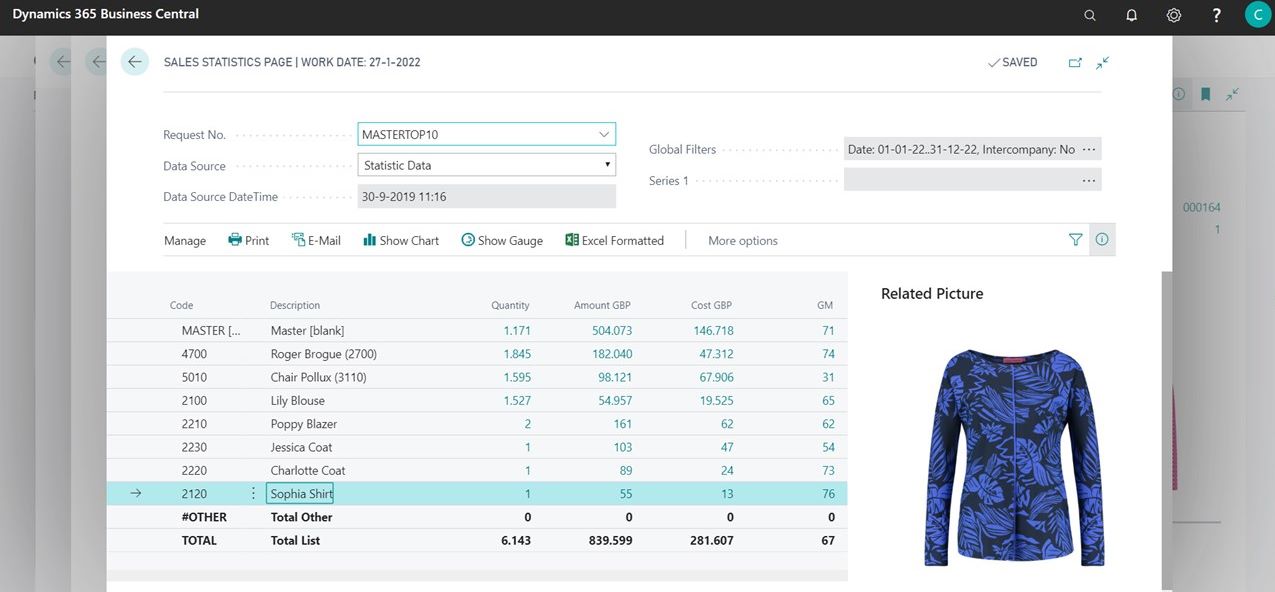
15. Product Lifecycle Management
Product Lifecycle Management (PLM) is a core function of Manufacturing ERP systems, enabling organizations to manage every stage of a product's life cycle, from conception to retirement:
- Collaborative Design: ERP systems facilitate collaboration among cross-functional teams involved in product design. This includes engineers, designers, and product managers, ensuring that everyone is on the same page.
- Version Control: ERP systems maintain version control for product designs and specifications. This prevents confusion and errors that can occur when multiple versions of product data are in use.
- Change Management: When changes are required during the product development process, ERP systems manage change requests, approvals, and implementation, ensuring that changes are well-documented and controlled.
16. Rapid Prototyping
Prototyping is a crucial step in product development, and ERP systems expedite this process:
- 3D Modeling Integration: ERP systems often integrate with 3D modeling and prototyping software. This allows for the rapid creation of physical prototypes, reducing the time required for design validation.
- Simulation and Testing: ERP systems enable simulation and testing of product designs virtually. This helps identify issues early in the design phase, preventing costly rework later on.
- Materials and Cost Estimation: ERP systems provide real-time data on the availability and cost of materials, aiding in the selection of cost-effective materials for prototypes.
17. Efficient Project Management
Effective project management is crucial for coordinating product development efforts, and ERP systems offer project management capabilities:
- Project Scheduling: ERP systems enable project scheduling, ensuring that tasks are completed in a coordinated manner. This reduces delays and accelerates project timelines.
- Resource Allocation: ERP systems help allocate resources to projects, ensuring that the right people and equipment are available when needed.
- Milestone Tracking: ERP systems provide tools for tracking project milestones and deliverables, allowing teams to stay on top of deadlines.
By implementing PLM features, supporting rapid prototyping, and facilitating efficient project management, Manufacturing ERP systems enable organizations to bring products to market faster, seize market opportunities, and respond to customer demands with agility. In the next section, we'll explore how ERP systems enable data-driven decision-making within manufacturing operations.
Enabling Data-Driven Decision-Making
In today's data-rich business landscape, the ability to make informed decisions is a critical factor in achieving success. Manufacturing ERP systems are equipped with robust analytics and reporting capabilities that empower organizations to harness data for better decision-making. In this section, we'll delve into how ERP systems enable data-driven decision-making within manufacturing operations.
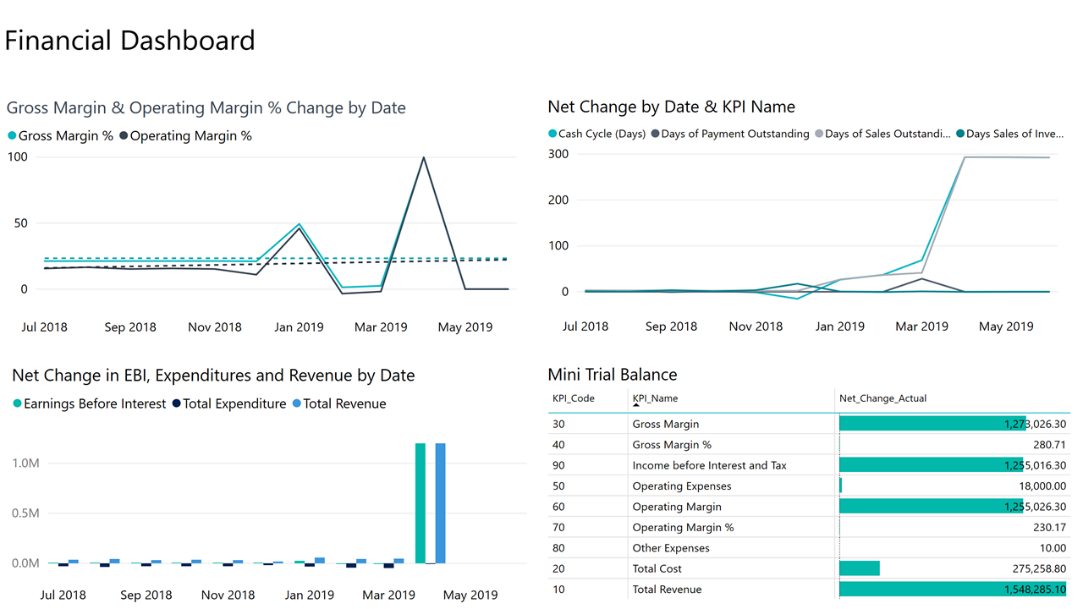
18. Business Intelligence and Analytics
Business Intelligence (BI) and analytics capabilities are integral components of Manufacturing ERP systems, offering a wide array of benefits:
- Data Visualization: ERP systems provide data visualization tools, such as dashboards and interactive reports, making complex data easily understandable. This allows decision-makers to quickly grasp important insights.
- Trend Analysis: BI tools within ERP systems enable trend analysis, helping organizations identify patterns in data over time. This is crucial for predicting market trends and adjusting production accordingly.
- Predictive Analytics: Some ERP systems incorporate predictive analytics, which use historical data and machine learning algorithms to forecast future trends and outcomes. This aids in proactive decision-making.
19. Key Performance Indicator (KPI) Tracking
KPIs are essential metrics for measuring the health and performance of manufacturing operations, and ERP systems provide tools for tracking and analyzing KPIs:
- Customized KPIs: ERP systems allow organizations to define and track customized KPIs that align with their specific goals and objectives. This ensures that performance metrics are directly tied to business priorities.
- Real-time KPI Monitoring: ERP systems offer real-time monitoring of KPIs, giving decision-makers immediate access to critical performance data. This enables rapid response to deviations from targets.
- Benchmarking: ERP systems often support benchmarking against industry standards and competitors. This helps organizations assess their performance relative to peers and identify areas for improvement.
20. Data-Backed Insights
ERP systems transform raw data into actionable insights, providing decision-makers with valuable information to guide strategies and tactics:
- Demand Forecasting: By analyzing historical sales data and market trends, ERP systems provide insights into future demand patterns. This informs production planning and inventory management decisions.
- Cost Analysis: ERP systems offer detailed cost breakdowns for products and processes, helping organizations identify cost-saving opportunities and allocate resources efficiently.
- Supplier Performance Analysis: ERP systems enable organizations to evaluate the performance of suppliers based on data-driven metrics, aiding in supplier selection and negotiation.
By leveraging BI and analytics capabilities, tracking KPIs, and deriving data-backed insights, Manufacturing ERP systems empower organizations to make informed decisions, optimize operations, and stay ahead of the competition. In the next section, we'll explore how ERP systems ensure compliance and adherence to regulations within manufacturing operations.
Ensuring Compliance and Regulation Adherence
Compliance with industry regulations and standards is a fundamental requirement in manufacturing, and non-compliance can result in costly fines and damage to the brand's reputation. Manufacturing ERP systems are equipped with features that help organizations maintain compliance and adhere to regulatory requirements. In this section, we'll explore how ERP systems ensure compliance and regulation adherence within manufacturing operations.
21. Regulatory Reporting
Manufacturing ERP systems provide tools for generating accurate and timely regulatory reports, a critical aspect for businesses in regulated industries:
- Automated Reporting: ERP systems automate the process of generating compliance reports, reducing the time and effort required for manual reporting. This ensures that reports are submitted on schedule.
- Data Accuracy: With centralized data management, ERP systems minimize the risk of data discrepancies in compliance reporting. Data accuracy is crucial for meeting regulatory standards.
- Audit Trails: ERP systems maintain detailed audit trails of data changes and user actions. This transparency is essential for demonstrating compliance and providing evidence during audits.
22. Audit Trails
Maintaining comprehensive audit trails is vital for regulatory compliance, and ERP systems excel in this area:
- User Activity Tracking: ERP systems record and trac
Liked what you just read? Sharing is caring.
October 13, 2023 by Frédéric Charest by Frédéric Charest VP of Marketing
Data-driven Growth Marketer with a Passion for SEO - Driving Results through Analytics and Optimization